Телефон: 8 (926) 549-82-18
Факс: 8 (926) 549-82-18
manager@nicstroy.ru
Прайс-лист, расценки, услуги
Цемент, цементные смеси, виды цемента
- 14.05.2009
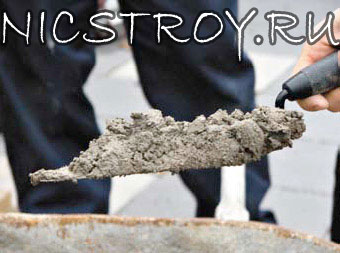
Основные разновидности цемента: шлаковый и глиноземистый, портландцемент. Распространены марки цемента: 200, 300, 400, 500 и 600. Временные характеристики схватывания цементов должны находиться в районе от 45 минут и выше, а завершение через 12 часов. Для полного отвердения необходимо 28 дней. В течение этого времени цемент набирает свои максимальные характеристики, показатели. Цемент используют для изготовления бетонов, растворов, строительных смесей, гидроизоляции и прочих строительных материалов.
Технология производства цемента
Цемент не является природным материалом. Его изготовление - процесс энергоемкий и дорогостоящий, однако результат стоит того - на выходе получают один из самых необходимых строительных материалов, он используется как самостоятельно, так и в в виде составляющего компонента других строительных материалов (например, бетона и железобетона) и смесей. Заводы по производству цемента, обычно, располагаются неподалёку от места добычи сырьевых материалов для производства цемента.
Производство цемента на заводах включает две стадии: первая - получение клинкера, вторая - преобразование клинкера в порошкообразное состояние с подмешиванием к нему гипса или других добавок. Первая стадия самая дорогостоящая, именно на ней базируется около 70% стоимости выходного продукта - цемента. Первая стадия - это добыча сырьевых материалов. Разработка известняковых месторождений происходит, как правило, сносом, то есть часть горы «сносят вниз», обнажая тем самым слой зеленовато-жёлтого известняка, который используется для производства цемента. Этот слой располагается, обычно, на глубине до 10 м (до этой глубины он встречается четыре раза), и по толщине может достигать 0,7-1 м. После этого этот материал направляется по конвейерной ленте на измельчение (стадия измельчени) до кусков равных 10 см в диаметре (стадия классификации). Далее известняк подсушивается (стадия сушки), и идет процесс помола (стадия дробления) и смешивания (применяется смесительное оборудование) его с другими компонентами, примесями. После этого эта сырьевая смесь подвергается обжигу. Так получают клинкер.
Вторая стадия также происходит в несколько этапов. Это: измельчение, дробление клинкера, подсушивание минеральных добавок, измельчение, дробление гипсового камня, помол клинкера вместе с гипсом и активными минеральными добавками. Однако стоит учитывать, что сырьевой (исходный) материал не бывает всегда одинаковым, да и физико-технические характеристики (такие как прочность, влажность и т. д.) у сырья различные. Поэтому для каждого вида сырьевого материала для изготовления цемента был разработан свой способ производства. Также же это способствует обеспечению хорошего однородного помола и полному перемешиванию компонентов. В цементной промышленности применяют три способа производства, в базовых положениях которых заложены различные технологические приемы подготовки сырьевого материала: мокрый, комбинированный и сухой.
Мокрый способ производства цемента
Мокрый способ производства цемента практикуют при изготовлении цемента из глины (силикатный компонент), мела (карбонатный компонент) и железосодержащих добавок (конверторный шлам, пиритные огарки, железистый продукт). Влажность мела при этом не должна превышать 29%, а влажность глины - 20%. Мокрым этот способ именован потому, что измельчение сырьевой смеси происходит в водной среде, на выходе получается шихта в виде водной суспензии (смеси) - шлама влажностью 30 - 50%. Далее шлам транспортируется в печь для обжига, диаметр которой достигает 7 м, а длина - 200 м и более. При обжиге из сырья выделяются углекислоты. Далее шарики-клинкеры, которые образуются на выходе из печи, размельчают в тонкий порошок, который и называется цементом.
Сухой способ производства цемента
Сухой способ состоит в том, что сырьевые материалы перед помолом или в его процессе подвергаются стадии сушки. И сырьевая шихта выходит в виде сильноизмельченного сухого порошка.
Комбинированный способ производства цемента
Комбинированный способ, как уже видно по названию, заключается в использовании и сухого и мокрого способа. Комбинированный способ имеет две разновидности. Первая состоит в том, что сырьевую смесь готовят по мокрому способу в виде шлама, потом её обезвоживают на фильтрах до влажности 16 - 18% и транспортируют в печи для обжига в виде полусухой массы. Второй вариант приготовления является прямо противоположным первому: сначала используют сухой способ для изготовления сырьевой смеси, а затем, добавляя 10-14% воды, гранулируют, размер гранул составляет 10 - 15 мм и подают на обжиг.
Для каждого из способов применяется определенный вид оборудования и строго определенная последовательность операций, действий.
Далее цемент фасуется, упаковывается в бумажные мешки по 50 кг. Отправка, доставка до складов производится на автомобилях или по железнодорожной дороге.
Без цемента, цементных смесей не обходится ни одно строительство, а это высокий показатель его отличных эксплуатационных характеристик.
Виды цемента
Армоцемент
Армоцемент - материал, состоящий из мелкозернистого бетона, в составе которого равномерно распределены проволочные стальные сетки. Применяют армирование двух видов:
- проволочными стальными сетками;
- стержневой арматурой.
Для усиления растягивающих усилий применяется армоцемент комбинированного армирования, содержащий сетчатую и стержневую (проволочную) арматуру. С использованием данного материала производят тонкостенные элементы: оболочки труб, дебаркадеров, резервуаров речных и морских судов; ограждающие и несущие конструкции толщиной 15-30 мм.
Глинозёмистый цемент
Глиноземистный цемент - быстротвердеющее гидравлическое вяжущее вещество.
Получение: В качестве исходных материалов для получения глиноземного цемента применяют известняк, известь или породы, с высоким содержанием глинозема (Al2O3).
Химический состав - CaO (минимум 36%), Al2O3 (минимум 35%), Fe2О3 (10 - 14%) и SiO2 (2 - 4%).
Получают глиноземный цемент в результате тонкого измельчения клинкера, получаемого обжигом (до спекания или плавления) сырьевой смеси, состоящей из известняков и бокситов, пород, богатых глиноземистым клинкером. Плавление и обжиг сырьевой смеси происходит в электрических, доменных, вагранках, или в вращающихся печах.
Виды глиноземистого цемента
- Обычный глиноземистый цемент (содержание Al2O3 до 55%, температура плавления сырья 1450-1480С)
- Высокоглинозёмистый цемент (содержание Al2O3 до 70%, температура плавления сырья - 1700-1750С)
Технические характеристики: Начало схватывания не ранее 45 минут, конец схватывания не позже 10 часов. Сроки схватывания могут быть изменены добавлением замедлителей твердения (буры, борной кислоты, хлористого кальция и др.) или ускорителей твердения (портланд-цемент, гипс, известь и др.). Характеризуется быстрым нарастанием прочности, повышенной стойкостью против коррозии в агрессивных средах (сульфатные воды, хлориды, серные соли, окись углерода, метан), высокая и высокой огнеупорностью (в смеси с огнеупорными наполнителями - хромитовая руда, магнезит, шамот).
При затвердевании бетона на глиноземистом цементе образуется большое количество тепла, что позволяет применять эти бетоны при отрицательных температурах до -10С без подогрева. Благодаря тому, что глиноземистый цемент является быстротвердеющим, уже через 15 - 18 часов позволяет вводить сооружения в эксплуатацию. Имеет повышенную плотность цементного камня, что способствует хорошей устойчивости бетона против агрессивных жидкостей и газов (агрессивные среды) по сравнению с бетоном на портландцементе. Позволяет получать растворы и бетоны большей водонепроницаемости, чем на обыкновенном портландцементе.
Глинозёмистый цемент применяется для для производства гидравлически твердеющих огнеупорных бетонов и растворов; при строительстве подземных и морских сооружений, где требуется повышенная стойкость к сульфатам; для тампонирования холодных нефтяных скважин; для производства штучных изделий и огнеупорных бетонов с огнеупорностью до 1700C; для производства сборных железобетонных изделий на строительных площадках и заводах ЖБИ, где глиноземистый цемент играет роль ускорителя твердения бетона; для заделки пробоин в судах речного и морского транспорта; применяется при срочных аварийных и ремонтных работах. Глинозёмистый цемент выпускают трех марок: ГЦ-40, ГЦ-50, ГЦ-60.
Гидрофобный цемент
Гидрофобный цемент получают в ходе тонкого измельчения портландцементного клинкера с примесями гипса и гидрофобизующей добавкой (мылонафт, асидол, олеиновая кислота, кубовые остатки синтетических жирных кислот, окисленный петролатум и др.). Добавка, вводимая в количестве 0,1-0,3% от массы цемента, образует на поверхности его частиц тончайшие (мономолекулярные) гидрофобные (отталкивающие воду и влагу) плёнки, уменьшающие гигроскопичность (поры, возможность проникать влаги в эти поры) цемента и поэтому защищающие его от порчи при длительном хранении даже в условиях повышенной влажности. Перед применением гидрофобный цемент смешивают насухо с песком, так как для нормального смешивания гидрофобного цемента с водой и наполнителями нужно, чтобы гидрофобная оболочка не была сплошной и чтобы она довольно просто разрушалась и нарушалась по ходу приготовления бетонной смеси. Зерна цемента очищают от гидрофобной пленки, которая служит и пластифицирующей добавкой.
Технические характеристики: Данный цемент характеризуется меньшим водопоглощением, большей водонепроницаемостью и морозостойкостью, чем обычный портландцемент; способен долгое время храниться даже во влажной среде без потери активности. Повышенное воздухововлечение гидрофобного цемента уменьшает прочность тяжелых бетонов, однако, при производстве ячеистых и легких бетонов это качество играет положительную роль. Бетонные смеси на гидрофобном цементе подвергаются меньшему расслаиванию, стойки к попеременному высыханию и увлажнению.
Тампонажный цемент
Разновидность портландцемента. Производят совместным тонким помолом клинкера, специальных добавок и гипса. Применяют в виде цементного теста, содержащего 40-50% воды.
Виды. Выпускают двух видов: для так называемых горячих (75С) и холодных скважин (22С).
Существуют и специальные разновидности цемента. По своему составу тампонажные цементы подразделяют на виды: цемент с добавками (Д20); цемент без добавок (ДО); цемент песчанистый (П50); цемент с добавками, регулирующими плотность цементной массы (утяжеляющими или облегчающими). Классифицируются по сульфатостойкости: на сульфатостойкий (ССТ) и обычный. По плотности подразделяют на виды: нормальной плотности; облегченный (О); утяжеленный (У). Утяжеляющие и облегчающие добавки не должны вызывать деструкцию (разрушение) и коррозию цементного камня. Сроки схватывания: начало не ранее 1 ч 45 минут, конец не позднее 6-18 часов в зависимости от марки.
Используют главным образом для тампонирования (цементирования) газовых и нефтяных скважин.
Асбоцемент (асбестоцемент)
Асбоцемент - цементный композиционный материал, который состоит из затвердевшего портландцемента, упрочненный асбестовым волокном. Применяют, в основном, хризотиловый асбест, не содержащий вредных примесей. Цементный камень отлично сопротивляется сжимающим напряжениям и плохо - растягивающим напряжениям. Введение 15 % тонковолокнистого асбеста, обладающего высокой прочностью на растяжение, на порядок повышает физико-механические свойства цементного камня.
Характеристики материала: Асбестоцемент обладает высокой прочностью на растяжение, долговечностью, водонепроницаемостью, огнестойкостью, низкой электропроводностью и теплопроводностью.
Применение. Применяют свыше 40 видов асбестоцементных изделий: плоские плиты - офактуренные и обыкновенные или окрашенные для облицовки стен; профилированные листы для обшивки стен и кровель; панели стеновые и кровельные с теплоизоляционным слоем для неотапливаемых и отапливаемых помещений; трубы безнапорные и напорные и соединительные муфты к ним; специальные изделия (санитарно-технические, вентиляционные короба, электроизоляционные и др.).